Crane is an important engineering machinery for material handling, its application areas are quite wide. Involving people’s production and life, industrial and mining enterprises, national defense construction, aerospace and many other aspects. Crane wheels as its walking mechanism in the implementation of the elements, is to bear the working load of the equipment and realize the key components of the material handling. Therefore, the calculation and selection of crane wheels are crucial to ensure the stability and safety of the machine.
In this paper, we will explain how to determine the working diameter of crane wheels through calculation and verify whether the load carrying capacity of the wheels meets the use requirements and other elements. Key parameters and calculation formulas are covered in the article to help you make the correct calculation and selection in the actual project.
The design, selection and production of wheelsets should meet the requirements of relevant national standards:
- GB/T3811-2008 《Crane Design Code》;
- JB/T6392-2008 《Crane Wheel》;
- YB/T5055-1993 《Crane Rails》;
- GB2585-2007 《Hot Rolled Steel Rails for Railroads》;
- GB/T699-2015 《High Quality Carbon Structural Steel》;
- GB/T11352-2009 《Cast Carbon Steel Parts for General Engineering Purposes》;
- GB/T1184-1996 《Tolerances for Shape and Position, Unannotated Tolerance Values》;
- GB/T1801-1999 《Limits and Fits Selection of Tolerance Zones and Fits》;
The following are the detailed steps for wheel calculation:
- Collect data: First, determine the working load of the crane wheel, track size, wheel and track contact form, institutional working level, walking speed, wheel material, etc.
- Apply the formula: use the formula, these parameters are correctly substituted into the formula.
- Calculation results: According to the data provided and the formula, the wheel is calculated and verified, and whether the result meets the requirements is derived from the calculation results and the judgment conditions in the formula.
Calculation formula of the wheel:
I. Determination of wheel fatigue calculation load:
In the formula
PC — wheel fatigue calculation load (N);
Pmax — the maximum wheel pressure during normal operation of the crane (N);
P
min — the minimum wheel pressure when the crane is working normally (N);
II.The wheel tread contact strength calculation:
Wheel and track contact form attached figure:
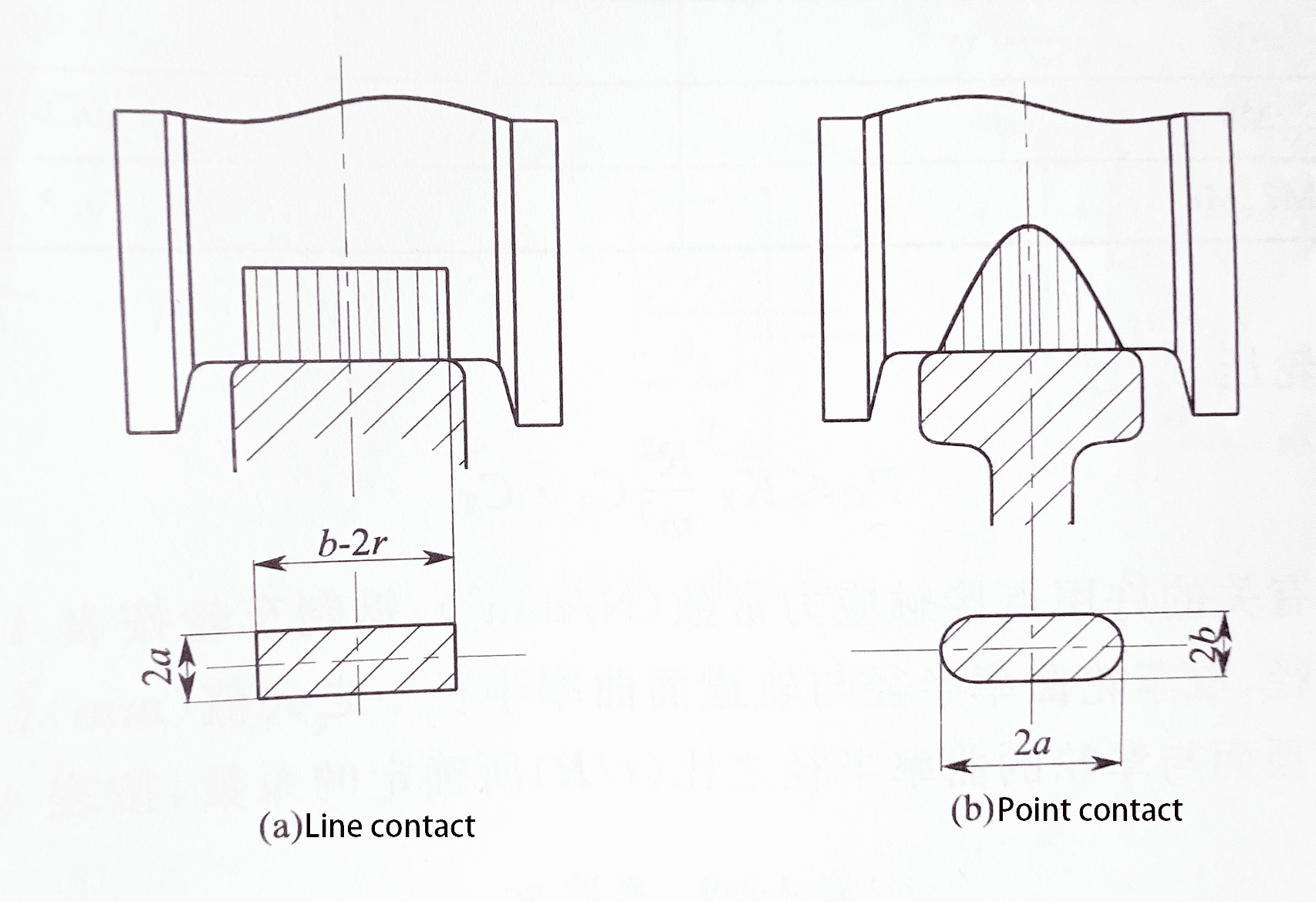
1. Allowable wheel pressure for line contact:
Pc≤K1×D×L×C1×C2
Where
P
C —- wheel fatigue calculation load (N);
K
1 —– material-related permissible line contact stress constant (N/mm2), selected according to Table 1;
D —– wheel diameter (mm);
L—— effective contact length between wheel and rail;
C
1—– speed coefficient, selected according to Table 2;
C
2—– working level coefficient, selected according to Table 3;
2. Allowable wheel pressure for point contact:
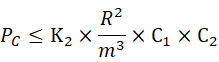
Where
P
C—- wheel fatigue calculation load (N);
K
2 —– material-related permissible point contact stress constant (N/mm2), selected according to Table 1;
R —– curvature radius, take the wheel radius of curvature and track radius of curvature in the larger value (mm);
M—— ratio of the top surface of the track to the radius of curvature of the wheel (r/R), selected according to Table 4;
C
1—– speed coefficient, selected according to Table 2;
C
2—– working level coefficient, selected according to Table 3;
Schedule of calculated coefficients:
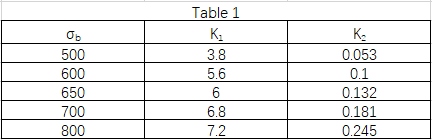
Note:
1. σ
b is the tensile strength of the material (N/mm
2);
2. Steel wheels should generally be heat-treated, tread hardness recommended for HB = 300 ~ 380, quenching layer depth of 15mm ~ 20mm, in determining the permissible value, take the σ
b when the material is not heat-treated;
3. When the wheel material adopts ductile iron; σ
b.≥500N/mm
2 material, K
1, K
2 value is selected according to σ
b.=500N/mm
2.

Note:
1. When r/R is any other value, the m-value is calculated by interpolation;
2. r is the small value of the radius of curvature of the contact surface
The above calculations can be used to verify the verification of the wheels of the set diameter, in order to determine the effective maximum bearing capacity of the wheels and the reasonableness of the dimensions (diameter of the wheels, wheels and rail with the dimensions, etc.).

Crane wheel set series attached chart:
Special types of crane wheel selection
Explosion-proof crane: explosion-proof crane wheel calculation method as above. Selection, according to the different levels of explosion-proof can choose a different surface form of the wheel. Such as when the explosion-proof level of Ⅱ C, the wheel tread and rim part should not be used due to impact, friction and ignition of explosive gas mixtures of copper alloy or other materials manufactured wheels. Generally, when the explosion-proof level is lower than ⅡC, the surface of the wheels should not be specially treated.
Important Notes
Please note the following important matters when making wheel selection calculations:
- Wheel type: Different types of wheels have different performance characteristics, so make sure to use the parameters of the correct type of wheel for calculation.
- Project requirements: Depending on the specific project requirements and ground conditions, it may be necessary to adjust the crane wheel diameter. Too small a wheel diameter may cause the machine to be unstable, while too large a diameter may increase the height of the machine and limit its range of use.
- Professional consultation: If you are unsure how to obtain the correct parameters or how to perform the calculations, consult a professional engineer or manufacturer who can provide detailed information about your particular crane.
In conclusion, calibration calculations for crane wheels are an important step in ensuring the safe and efficient operation of your machine during operation. By understanding the key parameters and applying the formulas correctly, you can effectively determine important information such as the wheel diameter and wheel load profile that is appropriate for your crane, thus improving the efficiency and safety of your engineering operations.